實用新型涉及一種工件加工設(shè)備,具體為一種電機軸孔加工設(shè)備。
背景技術(shù):
電機軸是電機產(chǎn)品的重要組成部分,電機軸的加工精度、質(zhì)量直接影響電機的整體質(zhì)量和使用壽命。如圖1a~1b所示,傳統(tǒng)的電機軸產(chǎn)品尾部錐孔加工通常采用普通車床通過人工操作方式進行加工,需要人工往夾具里上料,穩(wěn)定性差,效率低,且容易現(xiàn)廢品,存在導至廢品率高,加工精度低,勞動強度大等不足。主要缺點分為兩方面:
供料方面
1.效率低:由于頻繁的重復勞動會使人疲勞,人的精神狀態(tài)也會對生產(chǎn)效率造成影響,所以影響了從供料效率;
2.廢品率高:由于該產(chǎn)品有正反方向之分,一旦操作人員出現(xiàn)疏忽,就會造成廢品,同時受外界影響也會造成操作人員分神;
3.無法長時間連續(xù)工作:人工操作勢必會有休息時間,造成設(shè)備停產(chǎn);
4.精度低:人工操作不如機器穩(wěn)定,容易造成尺寸偏差。
加工方面
1.無法連續(xù)加工,每加工完成一個工件后需取下,再裝夾下一個工件,加工不能連續(xù)進行,間隔時間長,人員勞動強度大,生產(chǎn)效率低下;
2.設(shè)備穩(wěn)定性差,尺寸偏差大,易超差造成廢品;
3.夾頭裝夾效率低,無法滿足連續(xù)運行的需要;
4.加工后的工件需手動下料,浪費大量時間。
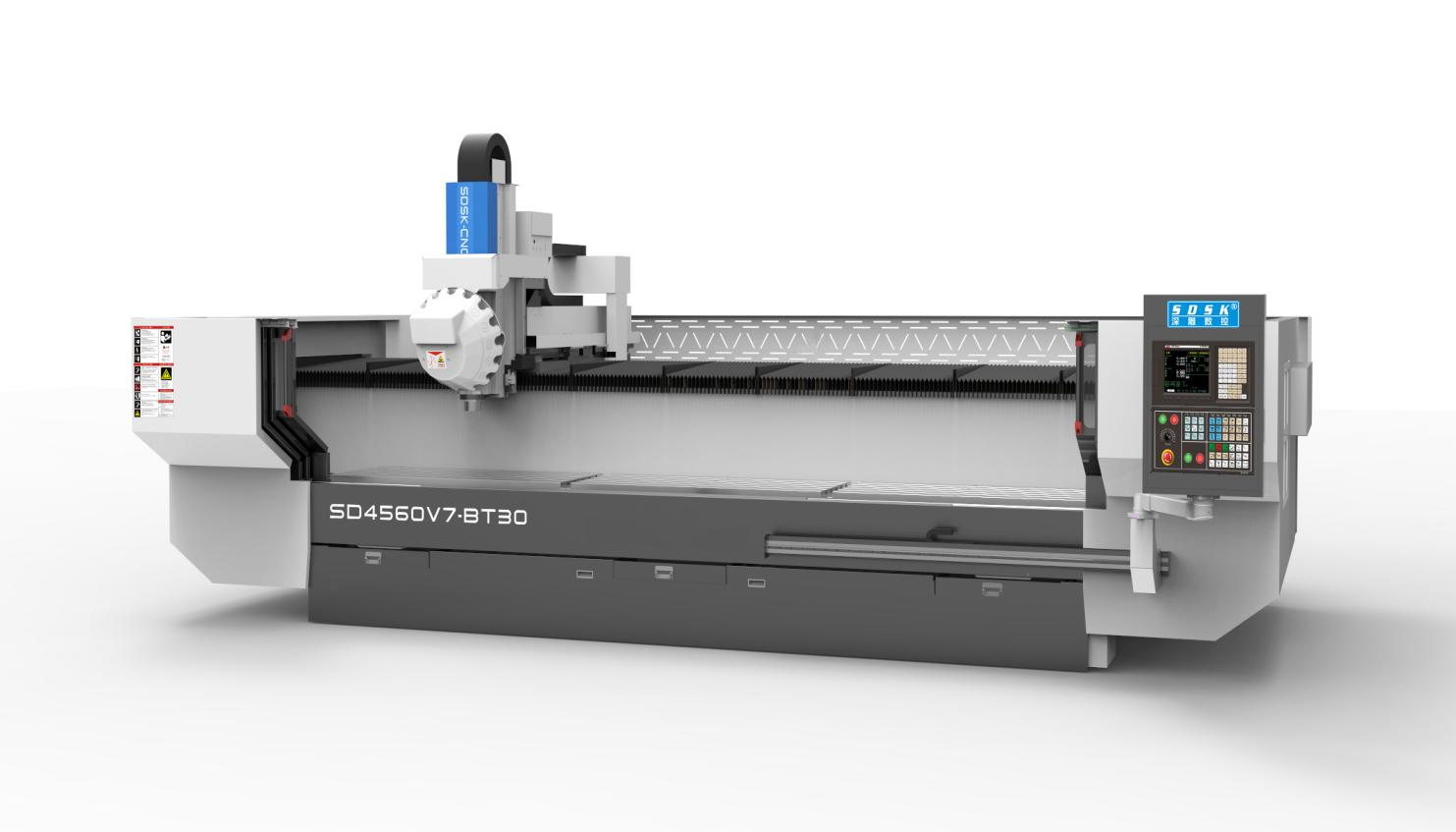
技術(shù)實現(xiàn)要素:
針對現(xiàn)有技術(shù)中電機軸產(chǎn)品尾部錐孔的加工過程勞動強度大、效率低等不足,本實用新型要解決的問題是提供一種可自動上料、卸料,加工連續(xù)、極大提高工作效率的電機軸孔加工設(shè)備。
為解決上述技術(shù)問題,本實用新型采用的技術(shù)方案是:
本實用新型一種電機軸孔加工設(shè)備,包括床體、機構(gòu)主體、切削液箱體、主軸冷卻液箱體以及配電箱,機構(gòu)主體安裝于床體上,配電箱安裝于床體一側(cè),切削液箱體、主軸冷卻液箱體安裝于床體中;機構(gòu)主體包括供料組件、鉆孔組件、工位轉(zhuǎn)換組件以及傳送帶,其中供料組件、鉆孔組件、工位轉(zhuǎn)換組件均安裝于床體的工作臺面上,傳送帶安裝于工位轉(zhuǎn)換組件的側(cè)邊,下料夾爪的正下方。
所述供料組件包括底座、v型槽導軌、推料氣缸、螺紋氣缸、伺服電機以及下料氣缸,其中底座固定于床體臺面上,底座上通過基板和導軌座安裝v型槽導軌;導軌座上還固定有光纖支架,光纖支架上安裝光纖連接板和光纖傳感器;光纖支架兩側(cè)分別安裝第一~二支架,料倉底板固定在第一~二支架中間形成料斗,工件置于料倉底板上;伺服電機通過電機支座安裝于一側(cè)支架上,伺服電機的輸出軸通過聯(lián)軸器及轉(zhuǎn)軸安裝一分料輪,分料輪兩側(cè)端面上安裝擋料板,轉(zhuǎn)軸前端通過軸承安裝于第一支架上,并通過軸端壓板、軸承壓蓋以及端蓋壓緊;推料氣缸通過推料氣缸座固定在導軌座上,推料氣缸前端通過連接桿安裝有推桿和螺紋氣缸;下料氣缸通過下料氣缸支架安裝于底座一側(cè),下料氣缸活塞桿通過氣爪連接板與一下料氣爪相連。
供料組件還具有分料輪下?lián)醢搴头至陷喩蠐醢?,安裝于分料輪上、下兩側(cè)、第一~二支架之間;
還具有料反檢測裝置,安裝于分料輪的分料輪上擋板上,包括檢測桿以及接近開關(guān),其中接近開關(guān)通過接近開關(guān)支架安裝在分料輪上擋板上,檢測桿一端與反置工件的外徑或正置工件的槽徑抵接,當反置工件與檢測桿抵接時,檢測桿另一端觸碰接近開關(guān)。